When is Process Mining useful?
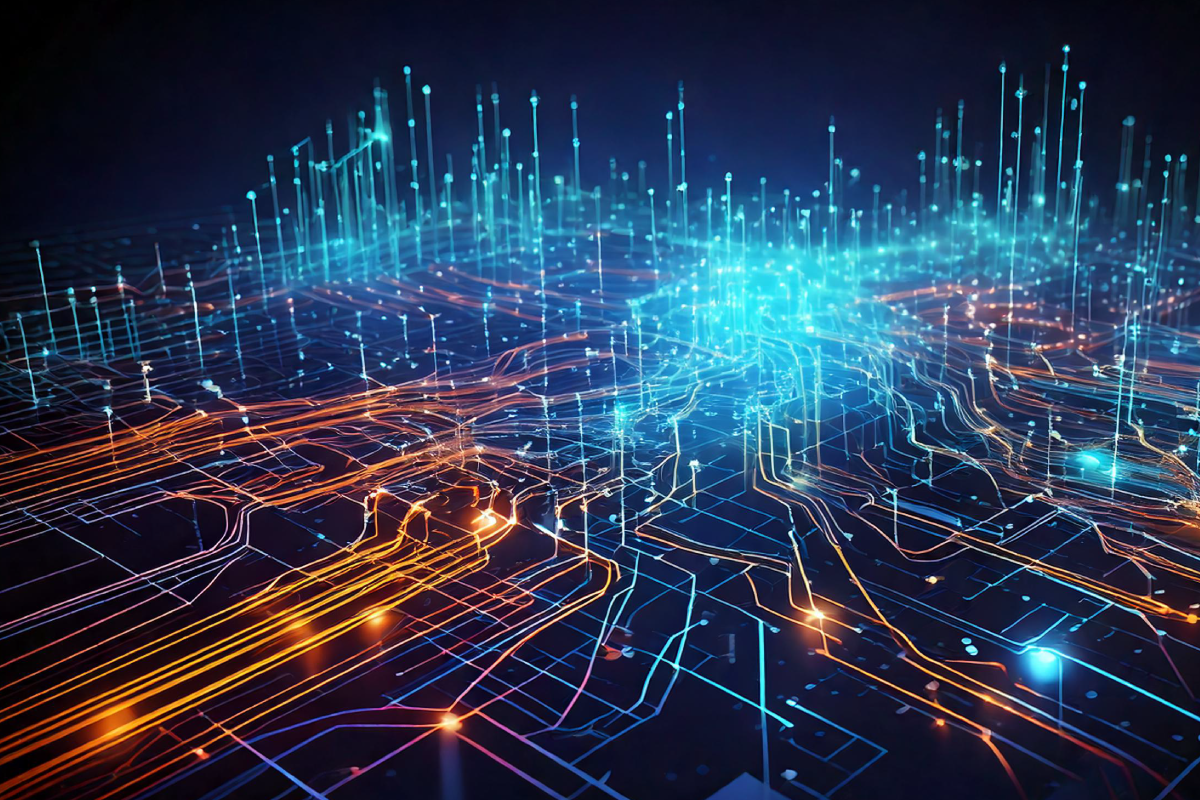
Companies use Process Mining to collect and analyze data from business processes. The collection and analysis of the data are partially automated, which paves the way for companies to optimize their processes quickly and cost-effectively. All in all, Process Mining is a technology that provides companies with a wide range of benefits.
In our blog post about application examples for Process Mining, we list several possible areas where this advanced technology can be applied. On this page, we provide further content explaining in which cases Process Mining is useful.
Greatest advantage: optimized processes and increased efficiency
Process Mining was primarily developed to optimize business processes and increase process efficiency. Therefore, the technology is useful when aligned with the relevant objectives. When organizations identify process problems or inefficiencies, Process Mining provides answers to questions such as:
- Where does the problem originate - i.e. from which department or process?
- What are the causes of the problem?
- What impact does the problem have on the business and on individual business units?
- Which employees or departments are involved in the problem?
Answers to questions like these are what differentiate Process Mining from Business Intelligence (BI) and comparable solutions and highlights the unique selling points and special features of Process Mining.
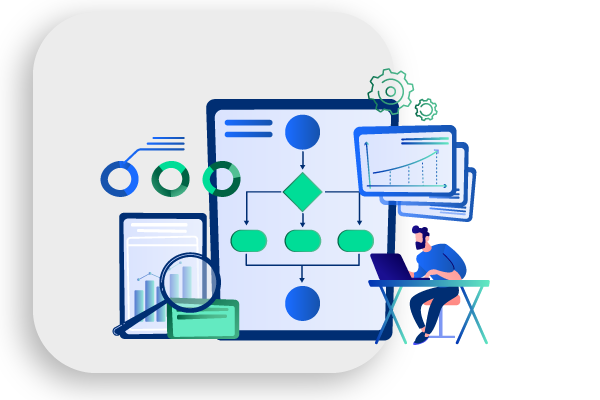
Differentiation from Business Intelligence and specifics of Process Mining solutions
BI provides insights into how problems and inefficiencies in processes affect a company's key performance indicators (KPIs). However, business intelligence does not provide information on how to resolve problems and inefficiencies.
Process Mining, on the other hand, examines and visualizes the processes exactly as they actually run. Process Mining tools retrieve their data from several programs and systems and provide an overview of the performance of individual processes in real time.
Particularly advanced Process Mining solutions even offer the option of analyzing several processes combined through Object-Centric Process Mining (OCPM), which measures performance at the interfaces of related processes. Furthermore, OCPM tools clarify the coherence between different processes; this is particularly valuable in terms of modern management methods such as Systemic Management.
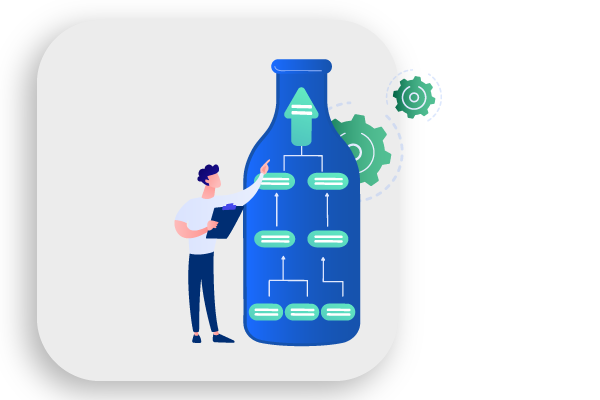
As-Is Analysis and detection of weak points
Process Mining tools include an As-Is Analysis that depicts the actual process flow with all variants and deviations. This visualization is often done in the form of a process flow diagram. This makes the actual process flows, bottlenecks, and loops clearly visible. The resulting high level of transparency makes it easier to identify weak points.
Bottlenecks are a common example of weak points. Using Process Mining, it is possible to pinpoint the steps in business processes where the flow gets stuck or where unnecessary delays happen. The analysis often shows which process steps take an excessively long time or where decisions are made that lead to time losses.
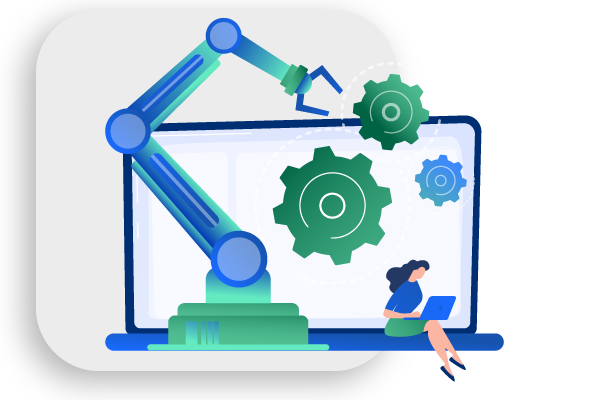
Uncovering potential for Robotic Process Automation (RPA)
Robotic Process Automation (RPA) is an additional feature for process optimization and the elimination of inefficiencies. Detailed analysis through Process Mining helps identify repetitive and time-consuming tasks and processes that are ideal candidates for automation.
RPA minimizes manual work steps and saves resources. These findings are particularly important for companies undergoing digital transformation. Thanks to these insights, the digitalization of business processes can be carried out much more effectively.
Use of Process Mining Technology for Compliance and Risk Management
Compliance managers and governance officers in organizations also benefit from Process Mining. In the areas of compliance and risk management, Process Mining ensures compliance with regulations and internal guidelines and identifies potential risks at an early stage.
A key factor to the use of Process Mining in compliance and risk management is the As-Is analysis of processes. The process flows are analyzed in a Process Mining tool not as they should be, but as they actually are. This provides insights into potential violations, weaknesses, and risks.
Controls and alerts in process flows
In Process Mining, business processes are compared with the prescribed target processes in real time. Deviations from how a process should run, e.g. with regard to the General Data Protection Regulation (GDPR), are thus identified more quickly. Thanks to the rapid comparison of As-Is and To-Be processes, deviations and compliance or legal violations are detected faster than in most other IT systems. In the case of violations, some Process Mining tools even generate automatic alerts. Thanks to these alerts, companies can respond quickly to critical situations and have better chances of preventing damage.
Detection, evaluation, and simulation of risks
Process Mining helps identify risks by highlighting areas where processes are insecure or inefficient. This can include the identification of weak points that entail compliance risks (e.g. missing controls or unsecured company processes). Subsequently, companies analyze and evaluate the existing weaknesses, which are conveniently displayed in the Process Mining software. Finally, companies can introduce measures to minimize risks.
A particularly useful feature is the risk simulation function. A good Process Mining tool can simulate certain risk scenarios within business processes. Based on these simulations, it can accurately assess weak points. The more precisely the risks are evaluated, the better priorities can be set when defining countermeasures, allowing the most significant threats to be addressed first.
A rarely seen side of Process Mining: Optimize customer service
When applying Process Mining, companies often focus on process optimization and efficiency improvements in production, collaboration, or order fulfillment (e.g., Order-to-Cash process). However, Process Mining is also insightful in customer service. It is particularly useful for the following purposes, among others:
- Determining and reducing waiting times by identifying throughput times and time-consuming customer service steps, among other things
- Improving the first contact resolution rate (FCR) by, for example, analyzing the frequency and background of follow-up inquiries in customer service
- Increasing customer satisfaction through, for instance, the holistic analysis of customer touchpoints using big data from multiple systems and tools
- Detecting and mitigating errors and complaints by, for example, analyzing the most common sources of errors or causes of complaints
Process Mining ultimately provides companies with comprehensive support in correctly utilizing data generated in CRM systems and on the website in the context of customer service. In this way, Process Mining becomes a key success factor in customer service process management.
Increased customer satisfaction leads to stronger long-term customer loyalty to the company, and the enhanced Customer Lifetime Value (CLV) reduces acquisition costs per customer. Ultimately, this increases the return on investment (ROI) and makes the overall marketing efforts more profitable.
Popular application area of Process Mining: Process Mining in production
One of the most common areas to apply Process Mining is in business processes within production. The effects of Process Mining mentioned earlier in this blog post regarding process optimization, increased efficiency, and automation of business processes can be seamlessly transferred to production as well.
In addition, Process Mining in production offers more opportunities, such as the more efficient use of resources and the optimization of machine maintenance. In the following sections, we will look at some selected effects of Process Mining in production.
More efficient use of resources
Process Mining provides insights into the scope for improving resource utilization (e.g., machines, personnel), enabling more efficient production planning. Advanced Process Mining software even takes into account seasonal fluctuations or specific demand periods, providing companies with the best conditions for optimizing the use of resources.
Production planning based on big data minimizes bottlenecks and overcapacity, which reduces production costs and increases planning certainty. In this way, companies benefit from more sustainable and cost-efficient production, which creates competitive advantages and increases profitability.
Optimization of machine maintenance
By analyzing data on machine usage, Process Mining can indicate impending breakdowns or maintenance requirements. Identifying signs of impending faults at an early stage allows preventive measures to be initiated. This is known as predictive maintenance.
By implementing predictive maintenance, companies reduce the risk of unplanned machine downtime. This helps maintain smooth production processes, ensuring that production targets are met and preventing delivery delays.
Improving processes in Supply Chains and Inventory Management
Process Mining can analyze and visualize the entire production flow, including material supply. Companies pursuing the goal of improving their inventory management therefore derive great benefits from Process Mining.
Optimized inventory management allows companies to reduce storage costs, avoid material shortages, and optimize material flow. A company's partners along the entire supply chain benefit from the outstanding reliability.
Adaptability and competitiveness
Thanks to Process Mining, companies can quickly respond to new internal and external challenges. This makes them competitive. Therefore, Process Mining is valuable for any company that aims to thrive in the highly competitive market in the long term.
Thanks to Process Mining, companies are able to react quickly to new internal and external challenges. This makes companies competitive. Therefore, Process Mining is valuable for any company that aims to thrive in the highly competitive market in the long term.
Companies also demonstrate their adaptability by deriving the right actions in response to the insights and information from the Process Mining software. After all, those who quickly adapt their business processes to new challenges are usually several steps ahead of their competitors.
Principle: For Process Mining to be effective, the necessary conditions must be met!
Successful Process Mining requires clear objectives, for example:
- Implement real-time compliance management;
- Uncover opportunities for automation in your business processes;
- or lay the foundation for predictive machine maintenance.
For Process Mining to be useful, not only do you need to have clear objectives, but you also need to meet the basic requirements. For example, without the digitalization of processes, Process Mining is not possible. Like Data Mining, Process Mining is also a purely digital technology that requires the digitalization of business processes in order to be applicable. If the processes are digitalized, then Process Mining is a largely uncomplicated method and analysis technique, as it obtains its information and data from the systems and tools themselves.
The digitalization of processes is just one of the basic requirements for companies to successfully use Process Mining. The specific prerequisites that processes must fulfill in order to be mapped, analyzed, and optimized using Process Mining software are described in detail in our article on the requirements for Process Mining.
FAQ: Questions and Answers on the Topic 'When is Process Mining Useful?'
Since Process Mining helps optimize digitalized business processes and improve their efficiency, its use is generally worthwhile. Companies with complex, extensive, and numerous business processes especially benefit from Process Mining, as there is significant potential for process improvement in such organizations.
This is a highly individual question so it is impossible to provide a general answer. We at mpmX are happy to provide you with individual advice as a professional service provider for Process Mining, and other solutions. In this consultation, we will discuss the optimization opportunities, as well as the anticipated costs and potential cost savings of implementing Process Mining in your company.